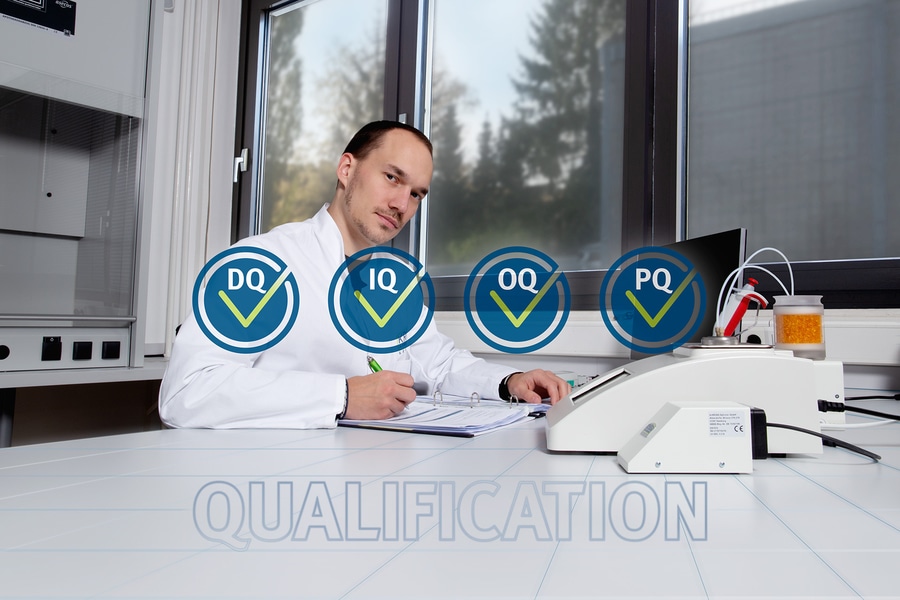
#Industry News
Qualifying and validating devices: In the past, present and future
DQ, IQ, OQ, PQ - Instruments of quality assurance and an important required from a standards perspective.
In recent years, the demand for qualification with manufacturer support has intensified significantly. For us at A.KRÜSS, it was clear that we could only meet this challenge holistically with customer support throughout the entire qualification process.In the past, validation and qualification in the laboratory was comparatively manageable: the proof that a technical system works flawlessly should be planned and confirmed in written form. Today’s stipulations are extremely high and elaborate. National and international laws and regulations, such as the German Act on Medical Devices (MPG) or the Code of Federal Regulations (CFR) of the American Food and Drug Administration (FDA), require validation for all processes, equipment and computerised systems related to product manufacturing. Good Automated Manufacturing Practice (GAMP) serves as a globally recognised validation guide.
Target setting DQ, IQ, OQ and PQ measures
The main target should be to guarantee a perfectly reproducible production in a defined quality and this with technically faultless facilities, equipment, utilities and processes and according to reproducible procedures.
An overview of qualifications of DQ, IQ, OQ and PQ
-The DQ is the documented proof that the planned design of the device is suitable for the intended use.
-The IQ confirms the complete specified delivery and installation in accordance with regulations. Devices and their parts are identified, device configuration is proven and manufacturer specifications are documented for trouble-free operation.
-The OQ verifies that the device is working according to plan and in accordance with regulations. Users receive, among other aspects, useful information for the SOP (Standard Operating Procedure) and user training.
-The final PQ is the performance check of the devices according to a defined procedure. It provides proof that the DQ process requirements are fulfilled under real conditions. The aim is to approve the device for laboratory use and to ensure that it meets the requirements of regulatory authorities, standards, guidelines, audits and internal quality assurance.
Modern device qualification
The entire process has raised many issues since its launch and is frequently subject to strong criticism, as the initially unspecific requirements for the individual qualifications led to an unprecedented variety of approaches. This often manifests itself in mountains of paper, immense effort, time delays in projects and huge additional costs. Even today, expensive qualified lab technicians are often and for long periods of time involved in the validation of equipment instead of focusing on their field of expertise. It is precisely during the support of the customer where the holistic A.KRÜSS qualification concept comes in. One of the primary objectives is the simplification of processes and the reduction of effort to a justifiable level. At A.KRÜSS, we do not only validate because we are obliged to do so, we do it to increase product quality and higher plant availability for the customer. We know that quality control in the laboratory must be executed in an effective and reliable manner. Trust in the quality and validity of analysis results is the basis for professional work in both normal and highly regulated areas.
The qualification models of A.KRÜSS
In addition to standard qualification, we offer an advanced solution: The PharmaKit was developed specifically for device implementation in highly regulated laboratories. This advanced solution includes the examination, commenting and conformity assessment of fixed written DQ requirements in the customer specifications. Furthermore, it includes the required upgraded qualification and documentary attestation of conformity with GAMP5, GMP, USP1058 and 21 CFR Part 11. All solutions of A.KRÜSS qualifications correspond with the “risk-based” approach which was introduced at the turn of the millennium. The equipment is checked and installed by our specialists with traceable test equipment. They have years of experience in the qualification of measuring instruments and know how the controls for the basic conditions of a routine operation must be defined. This ensures that the technology is suitable and works flawlessly. Our qualifications also include maintenance and calibration. Our specialists are equipped with the necessary special tools and measuring equipment and possess proven specialist expertise in test equipment management. The qualification also includes SOP (Standard Operating Procedure) consultation and employee training sessions carried out on the device of the respective employee. The qualification documents we use for validation comply with the latest specifications and standards. They can be examined by the customer before qualification on request. They comply with the requirements for effective comprehension, with clear structures and a standardised, modular document structure. As a result, processes can be carried out quickly and the documents are extremely precise. Of course, our qualification documents already meet the requirements for future GMP-compliant qualification with computer-assisted software solution.
The future of device qualification
In the early days of device qualification there was a regulatory change every three to four years. Since the turn of the millennium new guidelines and requirements for quality assurance are published almost every year. This is a development which will certainly proceed more rapidly, also with regard to digital transformation in the laboratory, where analysis and measuring equipment, sensors, processes and data will be linked in the future. Processes and structures are already being constantly reassessed. Institutions such as the Fraunhofer IPA are involved in the SiLA initiative (Standardisation in Lab Automation) on new communication interfaces, software solutions and standards. At A.KRÜSS we are observing these developments with excitement and interest and evaluating them for our process modifications. We always focus on the fact that our qualifications are a quality feature and can help to proactively implement future regulatory requirements.